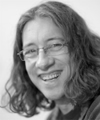
Simon Buddle explains that when space is at a premium, design teams can be tempted to place control panels in accessible locations, with adverse consequences for system maintenance.
We’ve spoken before about maintenance on jobs. It should be a standard part of everyone’s business. Systems, once commissioned and signed off, should naturally roll over into a maintenance contract. That contract will set out the frequency of visits and the checks to be carried out. Fine.
So here’s a question for all of you engineers out there: how many of you have had to dismantle the back of a wardrobe in order to access a control panel? My guess is probably every one of you. At some point, you’ll come across a project that has had the control electronics unceremoniously rammed into the back of a cupboard, in what the design team believes to be a great solution to a problem. This is because, in the UK, we suffer more than most with a lack of space in houses. Decade by decade, homes are shrinking. Some studies suggest that a new-build house is now 20% smaller than it was 40 years ago. That is at least a whole room.
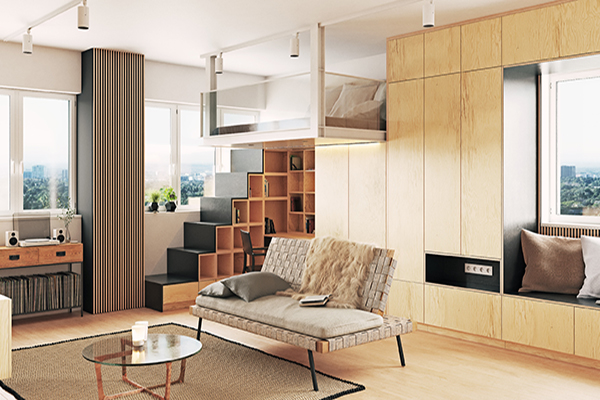
The space premium
Many years ago, whilst designing a 15m x 3m video installation in a swimming pool, I was given a stark lesson as to the value of space in a London town house. The owners wanted to have a live video image of a nature scene (think snow-capped mountains and rivers) projected on the side wall of their swimming pool. No problem; we just need three video projectors, a clever PC to run the video and a smart video controller to slice up the picture and send the relevant parts to the projectors. As I’m sure you can imagine, that little lot came with a chunky price tag. There was some concern about the cost, so to make savings, I suggested we create a false wall at one end of the pool to reduce the whole image size by 800mm. This in turn would mean we could use two projectors instead of three, thereby saving around GBP£15k. At which point I was castigated for reducing the value of the property by more than £180k! You see, the loss of nearly 1m x 5m x 3m at £12500 of usable/saleable space was not an option. This is why I ‘get it’ that space is at a premium in UK homes, especially in major cities.
Proper access to control panels
BUT, equally, good/easy access to the controls must be thought of as a prerequisite for any design. I’ve seen too many access hatches for air conditioning units where the hatch is only 300mm2, meaning you can get your head into the hatch or your arm and screwdriver but not both at the same time. So what do I care? Well, I’ve got wires I need to connect to the circuitry of the AC unit.
The design discussions around access to control panels must start with client access to electrical breakers. Most control panels have one or more isolator switches and RCD/RCBOs to protect the homeowner and the installation. These will, on the odd occasion, trip and have to be reset.
Think about your car’s fuse box. They are all clearly colour coded and the manual will contain a picture and index of which fuse controls which circuit, lights, heater, dashboard etc. That is our part of this equation, labelling accurately and documenting the control panel uses and buttons.
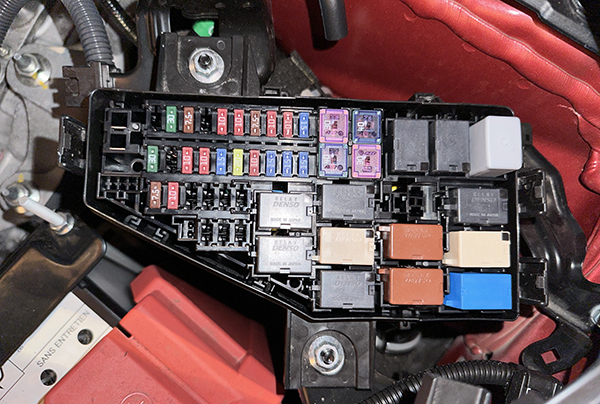
Indeed most KNX products have manual control buttons on the front, which is a great benefit if something goes horribly wrong. We can ask the client to press certain buttons or reset an electrical breaker – IF the panels are accessible that is. Recently, I took over a job where, floor by floor, the control panels are in void spaces above rooms. To do the straightforward process of resetting an electrical breaker requires a ladder, access hatch keys, a torch and control panel keys.
Now here’s the thing; just like fuses in a car, resetting an electrical breaker should be an easy job that any homeowner could do. All they need is good panel labelling and the knowledge as to where to find them. It should not require ladders, torches, etc.
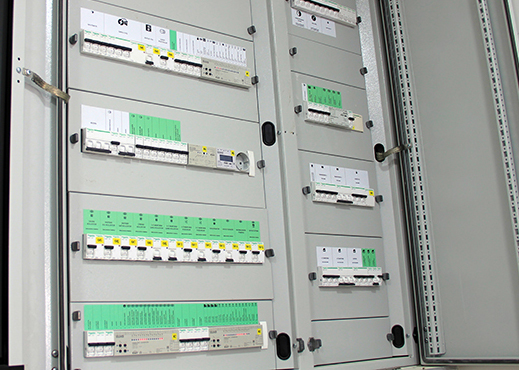
Conclusion
The fight for space within a property will continue forever. We are the people that interact with the control panels the most, but we are not the only ones. The discussion around access must be inclusive of end users. And of course access should enable people to do the relevant work whilst they are in front of the control panel.
KNX panels, as installed, offer many simple functions by way of local buttons on the front of actuators. During the design stage, it is vital that we take a stand and ensure proper consideration is given to the panels’ locations, as well as their ventilation, access, and manual controls. In so doing, we’ll ensure that the customer’s KNX experience is a positive one.
Simon Buddle CEng MIET, is a consultant for Future Ready Homes, a specialist in BMS and ELV services system design.