KNX UK Association Board Member Andy Davis discusses the implications of BS EN 15232 on achieving effective building automation and energy efficiency throughout the life-cycle of a building. He explains why KNX represents the most efficient means of implementing the approved Document and achieving Class A building performance.
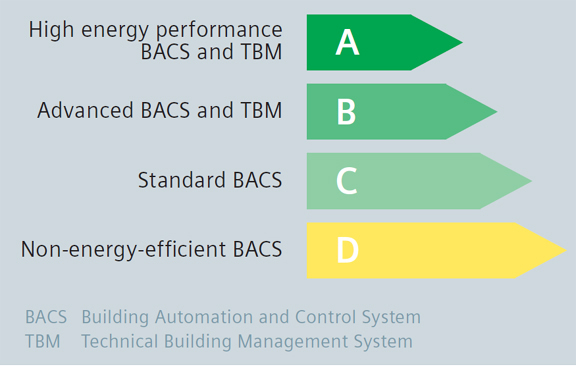
According to figures from the International Energy Association some 40% of the world’s energy consumption is taken up by the operation of buildings. The use of electricity and primary energy sources within buildings contributes to over 21% of global greenhouse emissions. In terms of a building’s actual life-cycle operational costs, energy accounts for around 50% spread over the 1-5 year design & build phase, a 20-40 year operational phase and 0-1 year demolition phase (based on figures from the DENA Congress, Berlin 2008). It is therefore clear that efficient energy usage within a building is essential at a time when energy costs continue to soar and a green approach is at the top of everyone’s agenda, from a residential property to an industrial facility employing 1000s of people.
KNX UK believes that during the operational life-cycle of a building, efficient energy usage can only be achieved properly if it is continually optimised with demand based BACS (Building Automation & Control System[s]) coupled with continual monitoring and adjustment of energy saving measures. With this approach, energy consumption can typically be reduced by up to 30%, based on BS EN 15232 and the energy saving that can achieved when going from a C Class to an A Class building and the thermal savings based on an office application.
According to the European Union Directive for Energy performance of Buildings (EPBD), the energy performance of a building means the amount of energy actually consumed to meet a building’s different needs for heating, hot water heating, cooling, ventilation, lighting and auxiliary energy. The European Union mandated CEN (European Committee for Standardisation) has standardised calculation methods in order to improve energy savings within CEN TC247. This has been approved to BS EN 15232 – 2012 Energy Performance of Buildings – Impact of Building Automation, Controls & Building Management. The BCIA, other companies and organisations are lobbying for a greater awareness of this Standard and the benefits it can bring building users in terms of energy savings.
BS EN 15232-2012 is just one of many regulations, laws and directives that impact upon buildings. The global aims of reducing energy usage are set out in the Kyoto agreement. Others include The Buildings Act 1984; The Building Regulations and its reviews (2006, 2010, 2013 and 2016); The Approved Documents of the Building Regulations (Part L – Conservation of Fuel 2010, Part F – Ventilation 2010, Part G – Sanitation/Hot Water 2010, Part J – Combustion Appliance 2010).
In BS EN 15232-2012, BACS energy performance Class A covers a building with automatic high energy performance building automation & control systems, TBM (Technical Building Management Systems) and include integrated individual room control, including demand control. Class B includes buildings with advanced building automation and control systems and TBM; Class C buildings have a standard building automation and control system only whilst Class D buildings have no energy efficient building automation and control system.
Different efficiency factors are also laid out for different types of buildings from offices, lecture halls and hotels, through to shopping centres, schools, restaurants, hospitals, industrial facilities and wholesale centres amongst others. Whilst all of these types of premises are recognised as having the potential to save energy, they are treated separately due to the way that they may be used, hours of occupancy and so on.
Different types of room may be included within one large building or plant and the control of energy supply with networked room automation based demand is key to maximum energy efficiency. For example, to turn an office from a Class C space to a Class A rating, the use of ventilation plant within a restaurant can be optimised through the use of time controls and air flow control using fans with variable speed drives. Lighting in an office can be improved from Class D to Class A by dispensing with manual switching in favour of automatically controlled lighting with presence detectors and the introduction of air quality sensors.
Research through simulation by FH Aachen University of Applied Sciences in Germany suggests that within shopping centres, this potential for savings is as high as 49% on typical current energy usage and in offices it is 39%, education buildings 34%, restaurants 31%, residential 27%, hotels 25%, and hospitals 18%.
KNX UK fully supports the use of demand led BACS to achieve Class A energy performance under BS EN 15232. It recognises too that the monitoring and analysis of building services’ performance is essential so that operational parameters can be continuously adapted and any additional measures can be decided upon. Carrying out practical energy saving activities such as regular planned maintenance, turning energy consuming device off/down, repairing faults and recycling components wherever possible are also essential.
So why does KNX provide the optimum approach to achieving Class A energy performance as outlined in BS EN 15232? In the traditional approach to building controls, it has not been uncommon for installations to be carried out by a number of different companies with many different sets of cables, materials, components, plant and tools. With the KNX open protocol system there is no need for different standalone separate systems. The traditional approach of treating every individual building control application separately is a thing of the past. Making different applications work together on one single bus network has many advantages. Linking lighting control, façade control, ventilation systems, underfloor heating and radiator zone control and smart metering altogether on the same bus network, allows them to share information about the space being controlled and provide the most energy efficient solution.
Consider an office with lighting control, fan coil unit heating/cooling, automatic blind control and perimeter low level heating, all being controlled on a single bus network. There is one wall mounted control device for the room temperature control, lighting scene set control and blind override as well as a single ceiling mounted presence detector for demand control. This installation may consist of a number of different manufacturers’ products, but the bus network will be common to them all. This makes both the specification of the products and their installation much easier.
When this form of integrated control is implemented across a large site, it becomes evident how major savings can be made over and above the traditional approach, while still maintaining a solid robust system. A key factor is that the building control system should be able to evolve and change as the building’s usage also changes over time. KNX intelligent building control systems are designed to cater for the changing needs of the building and offer suitable upgrade paths and expansion capability for the future.
KNX certified products are guaranteed to be completely interoperable between different manufacturers. The user has a vast range of products to select from and is not locked into any one supplier. Any installation is fully upgradeable and forwards compatibility is also guaranteed. With one integrated system only one contractor is required and there are standard commissioning procedures. Maintenance can be similarly managed more effectively by one contractor. There are increased levels of control and functionality provided by a lower number of wall mounted controllers as applications can share devices and data can be passed from one application to another.
However, if a proprietary system is installed, and after a time it needs to be repaired or parts replaced, there is no guarantee that the original component supplier or manufacturer will be able to support it.